
Service for Biacore™ 3000 Surface Plasmon Resonance (SPR) System
You rely on your equipment. Your equipment should rely on ATG.
Real-time monitoring and analysis of biomolecular interactions by SPR is an extremely sensitive technique. The Biacore™ 3000 is a world-class instrument, but without careful and regular maintenance, it is difficult to know if your results can be trusted. At Analytical Technologies Group, we want you to be confident in your results, your instrument, and your service provider. We keep the repertoire of instruments that we service small in order to maintain deep knowledge of all of them, ensuring that you are provided with the finest level of maintenance and repair.
Over 4,000 customers rely on ATG. You should too.
Tips for keeping your Biacore™ 3000 in good working order:
At the end of a day's work, run the Standby tool to keep buffer flowing at a low rate through the IFC
Do not leave the instrument overnight or longer with stationary buffer in the flow cells
If you intend to run Standby for an extended period, make sure that there is sufficient buffer in the buffer pack
To remove absorbed proteins, inclusion of 0.005% Surfactant P20 to sample and running buffer is recommended to minimize non-specific adsorption of material to the pump tubing and IFC channels
To prevent salt deposits accumulating in the liquid handling system, wash the connector block and the needle with deionized water once a week
A more extensive cleaning of all wetted parts within the fluidic system may be made using the Superclean service tool. This tool can be run if problems are suspected with the fluidic system
Having technical problems with your Biacore™ 3000 Series?
Fast Response
We provide very prompt responses to customers within one business day.
Fast Turnaround
Our field service engineers are expediently dispatched across North America & Europe to fulfill your service request.
Expert Staff
ATG’s highly trained, highly skilled staff ensure your instruments remain in optimal condition.
Parts In Stock
To minimize instrument downtime, we stock virtually all parts for the systems in which we specialize.
Biacore™ 3000 Troubleshooting Tips:
Sensorgram problems:
Low data quality is normal if the signal rises above about 80,000 RU (corresponding to a bulk refractive index of >1.40). This may be caused by injection of air which shifts the baseline so that the signal is outside the dynamic range of the instrument
Spikes in the sensorgram may be caused by small air bubbles in the flow cell. These may appear anywhere in the sensorgram
Signal drift may be caused by sample dispersion, carry-over of sample with a different bulk refractive index, matrix effects or conformational changes in the immobilized ligand. To minimize matrix effects, sample composition should be as close as possible to running buffer. Long-term drift may also result from unstable temperature at the flow cell
Shifts in signal baseline may be caused by small air bubbles developing in the flow cell and then breaking free into the buffer flow
Instruments problems:
If the air segments separating sample from buffer in the autosampler tubing are too large or appear to break up, air may be injected over the sensor surface giving a high signal outside the dynamic range of the instrument. In other autosampler operations such as Dilute, faulty air segments can lead to delivery of incorrect volumes
If the needle positioning is unsatisfactory for the injection port, wash station or rack positions (i.e. too high, too low or displaced to the side), check that the autosampler rack is correctly seated on the rack base, then run Service Tools: Needle replacement/positioning
Software Problems:
For problems with the Control Software which do not have a readily apparent solution, if possible, perform tests to determine whether the problem is reproducible and run the Software Problem Report in Service Tools to create a report including system-specific information. In the report, the nature of the problem and how you can reproduce it (or alternatively what you were doing when it arose) in as much detail as possible, and submit the report to GE Healthcare (the address is provided in the Software Problem Report utility).
If the software malfunction prevents you from running the Software Problem Report from Service Tools, the software problem report can be accessed from the software installation CD
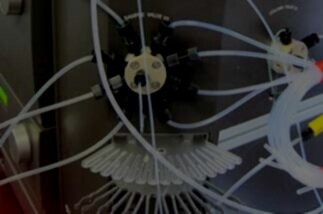