
Maintenance & Service for EL406™ Microplate Washer Dispenser
You rely on your equipment. Your equipment should rely on ATG.
The BioTek® line of microplate washers and dispensers are industry leaders, but even industry leaders need a bit of care now and again. If you have a BioTek® EL406™ Microplate Washer Dispenser, you can rely on ATG to provide the top-quality care that will keep your microplate washer running smoothly for many years. Our expert engineers and in-stock replacement parts ensure that we are ready and able to provide all of your service needs for the EL406™ and other BioTek® microplate washers / dispensers, whether you need preventative maintenance or an urgent repair.
Contact us and see why over 4,000 customers rely on ATG.
Tips for keeping your BioTek® EL406™ Washer Dispenser in good working order:
Daily maintenance is the key to keeping the liquid handler performing to its specifications. In the maintenance procedures provided within the Operator’s Manual, the requirements to use distilled (dH20) or deionized (DI) water can be met by numerous water purification methods, including MilliQ™. A minimum water purity of 2mOhm is expected.
Flush the washer and dispensers daily with an appropriate reagent or deionized water throughout the day. Routine rinsing helps to prevent the aspirate and dispense tubes from clogging between runs. Flushing the devices with deionized water is recommended at the end of the day for most applications.
Keep the devices clean and the tubing wet.
Prime the tubing to remove air bubbles and before dispensing. Priming the tubing is the most critical factor in assuring optimal performance.
For top performance and to preserve precious fluids, purge the fluid at the end of a dispense run and prime the tubing before dispensing. The tubing is permeable to air. When 20 minutes or more have elapsed between dispenses, or less than 20 minutes when using 1 μL cassettes, it is important to thoroughly prime the tubing before dispensing.
Check the external tubing connections for kinks and clogs.
Make sure the bottles, solutions, and tubing are clean and do not contain any particles or mold. Solutions that are recycled over several days will grow algae, bacteria, molds, or other undesirable organisms.
When a wash protocol leaves too much residual fluid in the wells, optimize the protocol with the following recommendations to improve evacuation: Add a secondary aspiration to a wash cycle, decrease the aspirate Travel Rate, add a Delay to the Aspirate and/or Final Aspirate step, or lower the aspirate height (Z-axis position).
The level of maintenance required to keep the instrument performing as expected is dependent on several factors, including the type of fluid dispensed, the frequency of use, and the work habits employed. Develop a maintenance schedule for your EL406™ based on the characteristics of the fluids used and the activity level.
Having technical problems with your BioTek® EL406™?
Fast Response
We provide very prompt responses to customers within one business day.
Fast Turnaround
Our field service engineers are expediently dispatched across North America & Europe to fulfill your service request.
Expert Staff
ATG’s highly trained, highly skilled staff ensure your instruments remain in optimal condition.
Replacement Parts Stocked
To minimize instrument downtime, we stock virtually all parts for the systems in which we specialize.
BioTek® EL406™ Washer Dispenser Troubleshooting Tips:
Most common problems can be avoided by daily/periodic cleaning and general maintenance.
If there is a manifold position error, the manifold movement is blocked. Check the dispenser height or Z-axis positioning (allow at least 1mm clearance above the plate), check for/remove any obstructions, or Contact Biotek TAC.
For uneven dispensing, make sure that all the cassette components are properly seated in their respective positions, the tips are not clogged, or whether the tubing needs to be replaced.
Vary the Flow Rate (experiment with different flow rates to determine which setting best forces fluid to break from the tip) to avoid viscous fluids sticking to the tips.
If the dispense tubes are not entering the well correctly, the microplate might not be properly seated or strips are not level, the horizontal dispense position does not align with the tubes in the wells, or the dispense tube(s) might be bent.
Should fluid be leaking from underneath the unit, check for a defective syringe cap, a leaking syringe seal, or a defective syringe piston.
If the dispenser is unable to dispense fluid, check to see if: the inlet tube is not connected at the manifold or at the bottle, the supply tube inside the supply bottle is kinked or disconnected, the dispense tubes on the manifold are clogged, the inlet tube is not connected to the bottom port of the syringe, the outlet tube is not connected to the top port of the syringe, or the valve flow direction is incorrect.
For aspiration tubes not entering the well correctly, check if: the microplate is not properly seated or strips are not level, the aspirate tubes position is too wide for a movement (change the horizontal, X- or Y-axis aspirate position in the protocol), or the aspirate tubes are bent.
If you are experiencing repeated blown fuses, the Vacuum Dissipate Delay might be set too low for the volume of the waste bottle or the pump has been flooded.
If there are scratches on the microplate bottom, the microplate dispense or aspiration height adjustment is too low, the microplate is not properly seated, or the strips are not level.
Should there be too much residual left in the wells after aspiration, check to see if: the vacuum filter is clogged, the waste bottle cover is not properly sealed or fittings are not properly connected, the manifold is out of alignment or not moving freely, the protocol requires optimization, or the aspirate tubes are bent.
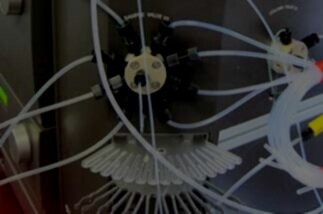