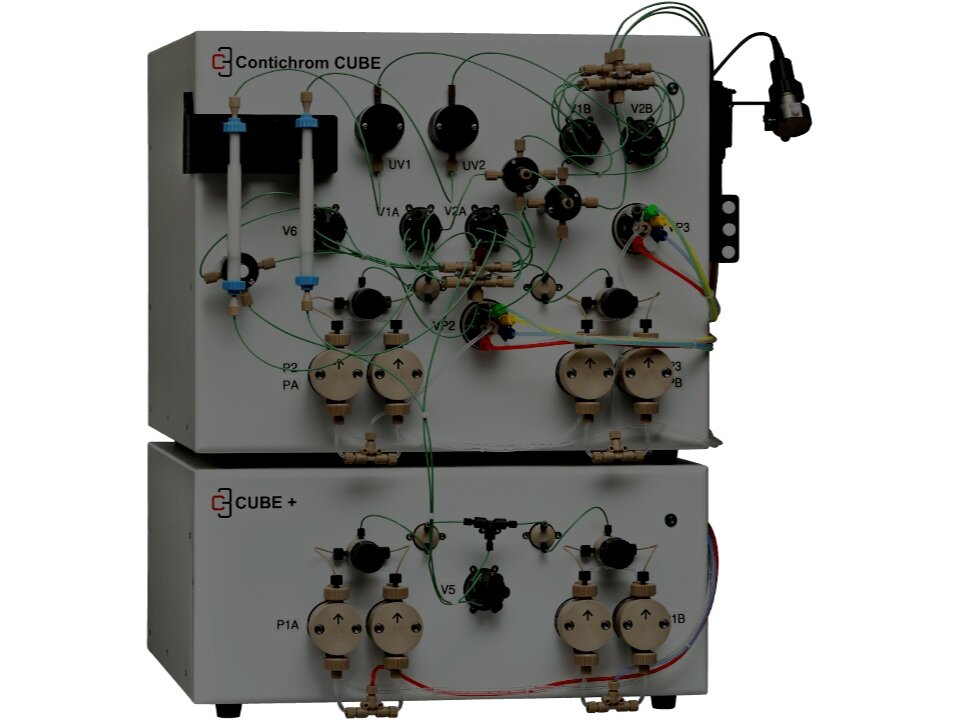
Maintenance & Repair for Contichrom® FPLC Systems
You rely on your equipment. Your equipment should rely on ATG.
Your FPLC is a critical part of your process development workflow, and when it goes down, you need to ensure it is back up and running quickly and any issues are resolved fully. That’s where Analytical Technologies Group comes in. We keep replacement parts in stock for Contichrom® CUBE, Contichrom® CUBE Combined, and Contichrom® Discovery FPLC systems to ensure we can get you back up and running quickly. Our deep specialization in FPLC instrumentation and focus on only a few product lines ensures that our engineers have the knowledge to identify your problem and solve it correctly the first time.
If you have a Contichrom® CUBE, CUBE Combined, or Discovery, contact ATG and see why over 4,000 customers and over 10,000 instruments rely on ATG.
Tips for keeping your Contichrom® CUBE FPLC in good working order:
If the system will not be operated for more than a full day, you should clean the system at the end of the last use. Remove the columns and replace them with union fittings, insert the inlet tubing into a bottle with at least 1 L of deionized water, and then run the cleaning procedure program.
Thorough cleaning of the system should be performed at least every six months. It should also be done when the product or project is changed, or before the system will be idle for a week or more. A thorough cleaning begins with a standard cleaning procedure, but has additional steps. After a standard cleaning is complete, run the cleaning program with at least 1 L of 1 M NaOH. Leave the NaOH in the system for 15 – 60 minutes, then run the cleaning program with 2 L of deionized water. Run the cleaning program with 20% acetic acid and leave it in the system for 15 – 30 minutes. Clean with 2 L of deionized water again, then with 1 L of 20% ethanol, leaving the ethanol in the system for 15 – 30 minutes. Finally, run the cleaning program with 2 L of deionized water.
Change the pump seal wash solution weekly. The solution should be 20% isopropyl alcohol or 30% ethanol in distilled water.
Calibrate the pH sensor weekly. It is recommended to calibrate using pH 4.0, pH 7.0 and pH 10.0 calibration solutions.
Replace the pump seals and pistons annually.
Replace the valve rotor and stator annually.
Many internal parts are polished or otherwise sensitive to potential dust and contamination. If you need to disassemble anything, be sure to work in a clean environment and set parts on a soft, lint-free surface.
Ensure all buffers and feed are filtered before use. Change buffers regularly to avoid microbial growth. Thoroughly degas all buffers before use.
Clarify samples by centrifugation or filtration prior to loading.
Having technical problems with your Contichrom® FPLC?
Fast Response
We provide very prompt responses to customers within one business day.
Fast Turnaround
Our field service engineers are expediently dispatched across North America & Europe to fulfill your service request.
Expert Staff
ATG’s highly trained, highly skilled staff ensure your instruments remain in optimal condition.
Replacement Parts Stocked
To minimize instrument downtime, we stock virtually all parts for the systems in which we specialize.
Contichrom® CUBE Troubleshooting Tips
If you experience lower than normal pressure or unstable pressure you may need to replace the pump piston seals. If you have leaks in the pumping system, it is very likely these seals require replacement. Depending on your process conditions, the seals normally last for approximately 1000 hours of run time. Be sure to condition the seals under pressure with an organic solvent (50% isopropanol in water is recommended) before resuming normal operation.
If you are experiencing issues with your pump check valves, it is likely due to particulate matter interfering with their operation, and cleaning them will resolve it.
The most common cause of ghost peaks or noisy signals is air bubbles in the system. Replace the column with union fittings and purge the system with equilibration buffer at 30 ml / min to remove the air.
If the signal intensity of the UV monitor is lower than expected or there are ghost peaks, it could be due to a dirty UV cell. Perform system cleaning.
An unstable conductivity signal or signal drift could be due to a dirty conductivity cell. Perform system cleaning.
Drift in the conductivity signal could also be due to changes in the temperature of the environment.
Baseline drift, waves in the signal, or a signal which does not return to the baseline could indicate an issue with the pump. This is true for both conductivity and UV signals.
If the signal does not respond as expected to a gradient, for instance staying low or increasing in steps, there could be air in the pump or a non-functional check valve.
A noisy pH signal is usually due to the flow cell, flow path, or buffer being dirty, or due to air in the system, although a malfunctioning pump could also cause this issue.
If the pH signal does not return to baseline after cleaning or re-equilibration, the re-equilibration time or flow rate could have been too low. Note that if there is an issue with the pump causing it to operate at too low of a flow rate, that could also cause this issue. It is also possible that the buffer used for pH re-equilibration was too weak.
If the pH reading is not correct and does not correct with calibration, the pH electrode needs to be replaced.
If the pressure signal has a slowly building drift, it is out of calibration. You will need to call for service, as this cannot be remedied by the user.
Overpressure is usually due to a blockage, often in a backpressure regulator, tube, or valve. If the pressure increases gradually over time, that is more often due to column fouling.
If pressure suddenly drops to zero it is likely due to air in the system. If it is not, the inlet check valves are likely blocked.
If fractions do not have the correct volume, check for spills. If there are spills, tubes were partially missed and you’ll need to use the wing screw on the fractionator head to fine-adjust its position. If there are no spills, it is likely an issue with the pump.
If your issues persist or you are unable to resolve them, ATG is here to help. Contact us for prompt and professional service.
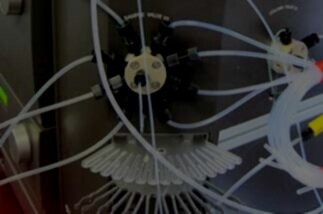