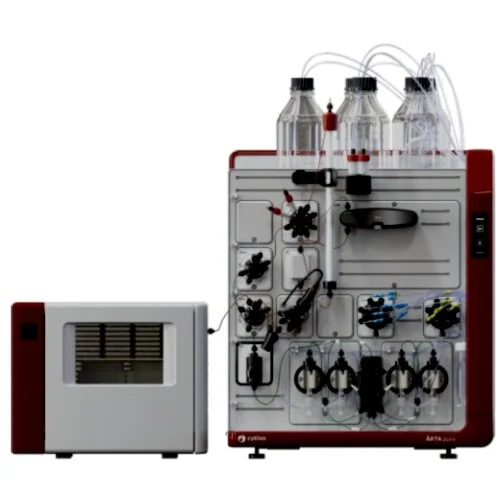
AKTA Pure Service & Repair
You rely on your equipment. Your equipment should rely on ATG.
Analytical Technologies Group specializes in the maintenance and repair of AKTA™ FPLC instruments such as the AKTA™ Pure. The AKTA™ FPLCs are one of a select few lines which we service, which ensures that our engineers are extremely knowledgeable about the AKTA™ Pure and other AKTA™ FPLCs. ATG also keeps AKTA™ Pure replacement parts in stock so we can minimize your downtime whenever you encounter a problem with your instrument. Our service contracts provide preventative maintenance and ensure your AKTA™ Pure will have a long, productive life.
You rely on your equipment. Your equipment should rely on ATG. Over 10,000 other instruments have!
Tips for keeping your AKTA™ Pure in good working order:
Most standard maintenance recommendations are tracked by the maintenance manager in the system control module of the UNICORN™ software. These are filled with factory default settings. These maintenance settings are there for a reason. Keeping to the recommended maintenance schedule will help prevent problems and ensure a longer life for your AKTA™ Pure.
The pH monitor should be calibrated daily before use. Calibration should use two buffers with a difference of at least one pH unit.
Pressure monitors should be calibrated weekly.
The pump rinsing solution should be changed weekly. Always use 20% ethanol in distilled water. Each rinsing system tube should be filled with 50 ml of the rinsing solution.
The fraction collector F9-C sensors should be cleaned weekly with 20% ethanol.
Once a month, check to ensure that the flow restrictor is generating the correct back-pressure.
The UV flow cell (U9-L) should be cleaned every six months using a 10% surfactant detergent solution (Decon 90, Deconex 11, or RBS 25 are recommended). Be sure to rinse thoroughly with distilled water.
The pH electrode should be replaced every six months.
Keep the instrument itself and the area around it clean. It is far easier to keep the area clean than it is to troubleshoot and repair internal components when a failure occurs.
When pH monitoring is not used, the pH electrode should be stored in a storage solution (1:1 mixture of pH 4 buffer and 1 M KNO3) inside the pH flow cell. If it is not going to be used for a week or longer, or if a week has passed since initially stored in storage solution, replace the pH electrode with the dummy electrode and store the pH electrode in storage solution.
Perform the system cleaning procedure following each use and leave the system stored in 20% ETOH to inhibit growth between uses.
Ensure all buffers are thoroughly degassed.
Avoid using old buffer solutions. Discard any buffer which shows signs of precipitation or microbial growth.
Having technical problems with your AKTA™ Pure?
Fast Response
We provide very prompt responses to customers within one business day.
Fast Turnaround
Our field service engineers are expediently dispatched across North America & Europe to fulfill your service request.
Expert Staff
ATG’s highly trained, highly skilled staff ensure your instruments remain in optimal condition.
Parts In Stock
To minimize instrument downtime, we stock virtually all parts for the systems in which we specialize.
AKTA™ Pure Troubleshooting Tips:
Most common measurement problems, such as baseline drift, ghost peaks, or general noise, are caused by the system being dirty or having air in it. A good first step to eliminate these causes is to clean the system and purge the lines. Degas all buffers before use. Centrifuge and / or filter your samples before loading.
Ensure there are no issues with the flow path. Check for leaks, twisted or kinked tubing, improperly connected tubing, and ensure the inlet tubing is correctly immersed in the buffer solution. Check to ensure the fraction collectors have been correctly prepared. If there do not appear to be issues with the flow path, inspect the inlet and inline filters for cleanliness, and check the back-pressure of the system. Change the filters to see if that fixes back-pressure issues.
If you have issues with the UV reading, check to ensure the UV monitor is set to the correct wavelength. Double-check that the wavelength being used is appropriate for your buffers and proteins. Ensure your UV lamp is turned on. You may also need to clean your optical fiber connectors, clean the UV flow cell, or remove dirt from the detector photo diodes.
If you cannot communicate with your system at all, ensure the correct system is selected in UNICORN™ system control. If you have other instrument communication issues, ensure all the node IDs are set correctly.
Ensure your columns are cleaned and prepared according to the manufacturer’s recommendations, and ensure that they are suitable for your target proteins.
If your system is stopping frequently but you are not experiencing any other issues, your air sensor sensitivity may be set too high. Set it to normal in the system settings.
Pressure or flow issues may be caused by obstructions in the flow path, leaking connections, or problems with the pump. Problems with pump pressure that do not have other noticeable causes (leaks, blockages, etc.) may indicate the pump springs, pistons, or piston seals require replacement. Leakage near the pump head is a definite sign that a piston seal or rinsing membrane require replacement or were improperly installed.
Issues with instability or noise could be caused by a malfunctioning mixer. If you place a stir bar above the mixer and activate the mixer, it should move. If not, the mixer may need replacement. You also may have problems if the mixer chamber size is not appropriate.
Temperature related errors, such as from the pump, valves, or mixer, could be caused by insufficient air flow to the instrument. Ensure the air intakes on the rear and left side of the instrument are unobstructed and have at least an inch of clearance. Ensure the room temperature is below 35°C. Turn the instrument off and wait for it to cool.
Many error codes may be cleared if the system is restarted. If the error code is not recurrent, it may have been a one-time issue which the system resolved by itself.
Regardless of the problem, do not open the covers or separation systems. Accessing or replacing parts that are not intended for user manipulation should only be performed by trained service personnel.
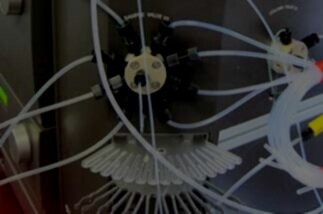