
AKTA Process Service & Repair
You rely on your equipment. Your equipment should rely on ATG.
Analytical Technologies Group has deep experience maintaining and repairing AKTA™ chromatography systems, including the AKTA™ Process. Our service engineers maintain exceptional knowledge of the AKTA™ Process and other instruments we service due to a narrow focus on just a few product lines. Our in-house stock of replacement parts ensures that we are ready to address just about any unexpected issues which may arise, ensuring that we can provide maintenance on short notice to keep your instrument downtime to a minimum. ATG also offers attractively priced service contracts to provide preventative maintenance and ensure your AKTA™ Process has a long, trouble-free life.
Tips for keeping your AKTA™ Process in good working order:
Auto-zero the UV monitor before each run. Regardless of process duration, this should be done at least once a week.
Clean and calibrate the pH electrode before each run. Regardless of process duration, this should be done at least once a week.
The in-line filter cartridge should be cleaned or replaced weekly if one is used.
The air sensors should be tested periodically. This can be done by running some air through the system, verifying that the alarm is triggered and the system is set to Pause.
The entire system should be sanitized once a week. Following the cleaning-in-place procedure in the manual.
Once a month, check the function of the air trap level sensor and calibrate it if needed.
Check the pump for oil leakage once a month. If there is leakage, call for service.
Once a month, perform a leakage test by running water or buffer through the system at maximum pressure. Replace any leaking seals.
A preventative maintenance inspection and testing of all sensors, instruments, pumps, and valves should be conducted annually by a trained service technician.
The complete system should be checked for rust and passivated with 5% phosphoric acid overnight if necessary.
The UV lamp should be replaced if problems arise due to low intensity or if UNICORN™ indicates a lamp failure.
Having technical problems with your AKTA™ Process?
Fast Response
We provide very prompt responses to customers within one business day.
Fast Turnaround
Our field service engineers are expediently dispatched across North America & Europe to fulfill your service request.
Expert Staff
ATG’s highly trained, highly skilled staff ensure your instruments remain in optimal condition.
Parts In Stock
To minimize instrument downtime, we stock virtually all parts for the systems in which we specialize.
AKTA™ Process Troubleshooting Tips:
Most common measurement problems, such as baseline drift, ghost peaks, or general noise, are caused by the system being dirty or having air in it. A good first step to eliminate these causes is to clean the system and purge the lines. Degas all buffers before use. Centrifuge and / or filter your samples before loading.
A noisy signal may also indicate impure buffer. Check to see if the signal is noisy when running deionized water.
UV signal problems could also be caused by bad UV cell cable connections, bad UV fiber connections, or a dirty UV cell. Check the connections and clean the cell.
Irregular flow, low flow, or unstable pressure could be caused by a check valve. A faulty check valve can be identified by observing the pressure trace. If they require cleaning, it can be done in place with 100% methanol or, if that does not correct the problem, in an ultrasonic bath with 100% methanol.
If a membrane valve sets off a valve alarm, or if it leaks, it likely requires cleaning. Pump 15 ml of 1 M NaOH at 10 ml/min through the pressure sensor then leave it for 15 minutes before rinsing thoroughly with deionized water. If that does not correct the problem, the valve should be dismounted and cleaned in methanol in an ultrasonic bath.
A non-responsive air sensor likely requires cleaning. Pump 15 ml of 1 M NaOH at 10 ml/min through the pressure sensor then leave it for 15 minutes before rinsing thoroughly with deionized water.
If there are signs of liquid leaking between the pump head and the housing side panel, if the volume of rinsing solution regularly changes, or if there is a reduction in flow accompanied by noise from the pump, you may need to replace the piston assembly, liquid chamber and/or ceramic tube including O-rings of the leaking pump head.
A wavy or non-linear conductivity gradient may be due to mixer motor malfunction. Start the system at a low flow rate. You should be able to hear the mixer motor as well as feel vibration from it if you place a finger on the mixer chamber housing.
If the conductivity value seems incorrect, it could be improperly calibrated. Recalibrate the conductivity cell and ensure the 1.00 M NaCl calibration solution is correctly prepared.
An incorrect conductivity reading could be due to the temperature compensation not being properly set or the column not being equilibrated.
High back pressure could be caused by dirt in the flow path. This could be due to injection of dirty / unfiltered samples. Ensure samples are filtered. Clean the flow path, valves, and sensors as necessary.
Regardless of the problem, do not open the covers or separation systems. Accessing or replacing parts that are not intended for user manipulation should only be performed by trained service personnel.
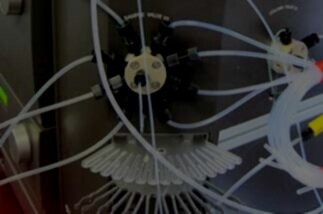