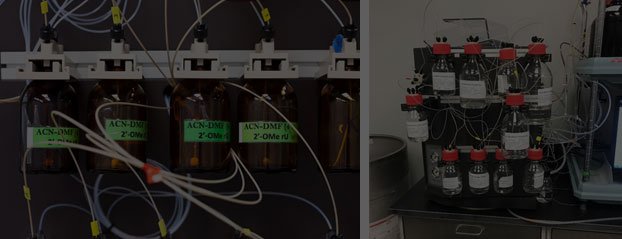
Service for AKTA OligoPilot Oligonucleotide Synthesizers
You rely on your equipment. Your equipment should rely on ATG.
Analytical Technologies Group has deep expertise maintaining and repairing AKTA™ instruments, including the AKTA OligoPilot™ oligonucleotide synthesizer. We are able to perform rapid repairs due to keeping parts on hand and having only the most knowledgeable field service engineers who specialize in only a small number of product lines. See why over 4,000 customers trust ATG to ensure their AKTAs and other instruments have a long, productive life.
Tips for keeping your AKTA OligoPilot™ in good working order:
Daily:
Inspect the P900 pumps and the system for leakages.
Wash the system flow path.
Calibrate the pH electrodes (optional)
Weekly:
Check the inlet filters visually and replace them if necessary.
Check the connectors in the bottle cap and on the inlet panel for tightness.
Replace the on-line filter.
Change the rinsing solution. Always use acetonitrile as rinsing solution.
Monthly:
Check that the FR-902 flow restrictor generates a back pressure of 0.2 ± 0.05 MPa.
Inspect the pressure relief valve for leakage.
Yearly:
Check the valve for external or internal leakage. Replace channel plate and distribution plate yearly or when required.
Replace the sealings.
Having technical problems with your AKTA OligoPilot™?
Fast Response
We provide very prompt responses to customers within one business day.
Fast Turnaround
Our field service engineers are expediently dispatched across North America & Europe to fulfill your service request.
Expert Staff
ATG’s highly trained, highly skilled staff ensure your instruments remain in optimal condition.
Parts In Stock
To minimize instrument downtime, we stock virtually all parts for the systems in which we specialize.
AKTA OligoPilot™ Troubleshooting Tips:
Many problems are caused by a dirty cell, leaking connections, or air in the line. Check your connections, clean your cell(s) and filters, and purge your lines to remove air.
UV curve problems are generally caused by issues with the UV cell. Especially if the autozero level is above 1000 mAU at 280 to 290 nm, you likely need to clean the cell. Other possible issues could be clogged end-line filters, poor UV fiber connections, or air in the pump or the cell. If the flow restrictor does not generate a back-pressure of 2.0 ± 1 bar at 10 mL / min flow, you likely have an air problem.
Conductivity problems are often caused by a dirty flow cell, leaks, or air in the line. If your reading is unstable or erratic, that could indicate a loose conductivity flow cable connection or problem with pump or valve function. If you cannot readily determine another issue, test the conductivity cell with KCl and NaCl (see the manual for more info). If your conductivity monitor fails the tests, it needs to be recalibrated or, if it cannot successfully be recalibrated, replaced.
If you see liquid leaking Liquid leaking between the pump head and the side panel, replace or re-install the piston seal or rinsing membrane.
Erratic pump pressure can have a number of causes, including air trapped in the pump heads, partially blocked solvent filters, leaking connections, piston seal leakage, a malfunctioning check valve, or a damaged piston. You can identify a malfunctioning pump head by observing the piston stroke indicator in the Check menu in UNICORN together with the pressure trace.
High system back pressure can be caused by dirty column frits, blocked/bent tubing, a blocked flow cell, a blocked flow restrictor, or overloaded columns.
If you get a “No Peak detected” message in UNICORN while in pause mode, perform the following checks:
Check and refill reagent bottles
Check the amidite bottles for damage or dirt, replacing damaged bottles and cleaning with acetone where necessary
Check the flow circuit for leaks
Check if the orange detritylation peak elutes properly. If not, restart the synthesis.
Check if the detritylation bottle is empty
Check if the amidite tubing is blocked. If so, install new tubing and clean the slider.
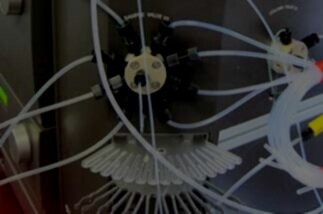