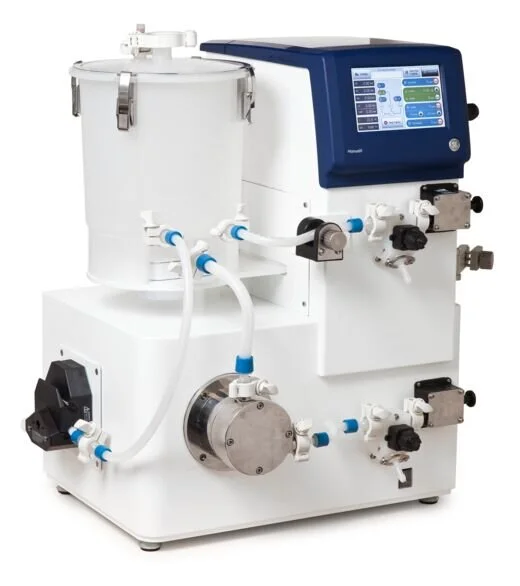
AKTA Flux Service & Repair
You rely on your equipment. Your equipment should rely on ATG.
Analytical Technologies Group are experts in maintenance and repair of the AKTA™ Flux and other AKTA™ systems. Due to our focus on servicing a narrow range of products, our engineers maintain expert knowledge on the AKTA™ line, and we always keep most commonly needed parts in stock so we can meet potential needs for emergency repairs. Over 4,000 customers trust ATG to ensure their instruments have a long, productive life. Work with us and you’ll quickly see why you should as well.
Tips for keeping your AKTA™ Flux in good working order:
Keep the instrument itself and the area around it clean. It is far easier to keep the area clean than it is to troubleshoot and repair internal components when a failure occurs.
At the end of the day, rinse the pump and system with distilled water. If you will be leaving the system for longer than overnight, remove the pH electrode and follow up with a rinse with 20% ethanol in distilled water.
Run the cleaning-in-place (CIP) protocol at least once per week, including any time prior to the instrument not being used for an extended period of time (such as over the weekend).
Regularly check for leakage on the system. Test for leaks by running at maximum operating pressure. Replace any seals or O-rings around leaking connections.
To prevent leaks before they occur, it is recommended that all gaskets, O-rings, and diaphragms are replaced annually.
All wearable parts on the peristaltic pump should be replaced annually.
Always empty the system and clean the system and filters after every run. You should not perform back-to-back runs.
If you will not be using the system for an extended period of time, including over the weekend, you should fill it with 20% ethanol in distilled water. This 20% ethanol storage solution should be flushed and replaced weekly while not in use.
Having technical problems with your AKTA™ Flux?
Fast Response
We provide very prompt responses to customers within one business day.
Fast Turnaround
Our field service engineers are expediently dispatched across North America & Europe to fulfill your service request.
Expert Staff
ATG’s highly trained, highly skilled staff ensure your instruments remain in optimal condition.
Parts In Stock
To minimize instrument downtime, we stock virtually all parts for the systems in which we specialize.
AKTA™ Flux Troubleshooting Tips:
Most common measurement problems, such as baseline drift, ghost peaks, or general noise, are caused by the system being dirty or having air in it. When in doubt, clean the system and purge the lines. Ensure all buffers are thoroughly degassed before use.
Ghost peaks in the UV curve could both be caused by a malfunctioning mixer. Check that it is functioning properly by placing a magnetic stir bar on top of the mixer housing; it should rotate when the system is in “Run” mode. Check that the correct chamber volume is being used.
A poor UV signal could also be caused by impure buffer. Purge the pump, run a system wash, and test the signal with ultrapure water to see if it gives a clean signal.
Conductivity baseline drift could be caused by a change in ambient temperature. If needed, use a temperature compensation factor. It could also be caused by leaks, improper mixer function, a dirty flow cell, or a non-equilibrated column.
Wavy conductivity gradients may be due to pump problems, although it can also be due to the mixing chamber. Contamination, insufficient chamber volume, and mixing motor failure can all be causes.
An incorrect or unstable conductivity reading could have a number of causes: A) the pump may not be operating properly, B) if temperature compensation is being used, the temperature sensor may not be calibrated or the temperature compensation factor may be incorrect, C) the column may not be equilibrated or may be dirty, D) the mixer may be malfunctioning, or E) the conductivity flow cell cable may not be connected properly.
Problems with the pressure curve could indicate a number of things. There could be air bubbles in the pump, in which case check for leaks and ensure there is sufficient eluent in the reservoirs. The pump valves may not be functioning properly, which may be solved by cleaning. The piston seal may be leaking and in need of replacement. The flow path could be blocked, which may be fixed by flushing it, replacing tubing, and / or filtering your buffers or samples prior to use.
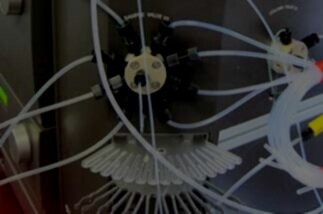