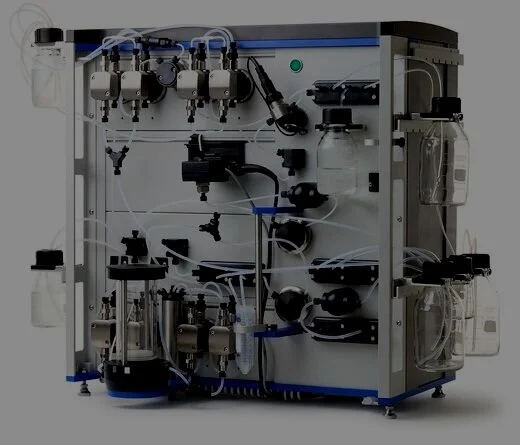
AKTA Crossflow Service & Repair
You rely on your equipment. Your equipment should rely on ATG.
Analytical Technologies Group has deep expertise maintaining and repairing AKTA™ instruments, including the AKTA™ Crossflow. We are able to perform rapid repairs due to keeping parts on hand and having only the most knowledgeable field service engineers. See why over 4,000 customers trust ATG to ensure their instruments have a long, productive life.
Tips for keeping your AKTA™ Crossflow in good working order:
Keep the instrument itself and the area around it clean. It is far easier to keep the area clean than it is to troubleshoot and repair internal components when a failure occurs.
At the end of the day, rinse the pump and system with distilled water. If you will be leaving the system for longer than overnight, remove the pH electrode and follow up with a rinse with 20% ethanol in distilled water.
The pH electrode should be removed and stored in a storage solution (1:1 mixture of pH 4 buffer and 2 M KNO3) when not in use. Replace the pH electrode with the dummy electrode. Never leave the pH electrode in the cell holder if the system will not be used for more than one day.
The pH electrode should be replaced every six months or if response time becomes slow and is not improved by cleaning.
Having technical problems with your AKTA™ Crossflow?
Fast Response
We provide very prompt responses to customers within one business day.
Fast Turnaround
Our field service engineers are expediently dispatched across North America & Europe to fulfill your service request.
Expert Staff
ATG’s highly trained, highly skilled staff ensure your instruments remain in optimal condition.
Parts In Stock
To minimize instrument downtime, we stock virtually all parts for the systems in which we specialize.
AKTA™ Crossflow Troubleshooting Tips:
Most common measurement problems, such as baseline drift, ghost peaks, or general noise, are caused by the system being dirty or having air in it. A good first step to eliminate these causes is to clean the system and purge the lines. Degas all buffers before use. Centrifuge and / or filter your samples before loading.
Select the appropriate membrane for your application. For cell processing, you want a membrane with a pore size 10x larger than your target protein’s longest dimension, but otherwise as small as possible. For concentration and diafiltration, select a membrane with a molecular weight cutoff 3-5x smaller than your target molecule.
If you recently changed anything about your process (buffer, membrane, etc.), did you remember to clean the system before performing any runs? Rinse the flow path and run the system sanitization method. Clean the filter by the cleaning-in-place method or by water flush method. Perform a water flux test. Buffer condition the filter.
Clean the inlet and outlet check valves if you experience irregular flow, low flow, or unstable pressure traces.
Clean the membrane valves if the membrane does not open or close properly or if internal leakage appears.
If the pH response time becomes slow but the electrode is not yet six months old, it can be cleaned. The cleaning procedure will vary based on what it is soiled with. A dry pH electrode can sometimes be regenerated by placing it in a 1:1 mixture of pH 4 buffer and 2 M KNO3 overnight
Irregularities in conductivity measurements may indicate that the conductivity cell requires cleaning. Pump 15 ml of 1 M NaOH at 10 ml/min through it using a syringe, leave it for 15 minutes, then flush with 500 ml of deionized water.
Pressure measurement irregularities may be due to a dirty pressure sensor. The pressure sensor can be cleaned by pumping 15 ml of 1 M NaOH at 10 ml/min through it using a syringe, leaving it for 15 minutes, then flushing it with 500 ml of deionized water. If that does not work, dismount the pressure sensor and clean it in an ultrasonic bath while the connections are immersed first in methanol then in distilled water.
When disconnecting connectors, ensure that the o-ring is still attached. O-rings which have separated from the connector and remain stuck in the port are a common cause of leaks.
Pressure or flow issues may be caused by obstructions in the flow path, leaking connections, or problems with the pump. Problems with pump pressure that do not have other noticeable causes (leaks, blockages, etc.) may indicate the pump piston, glass tube, liquid chamber, or O-rings need to be replaced. Leakage between the pump head and instrument panel is a clear sign that one or more of these parts require replacement.
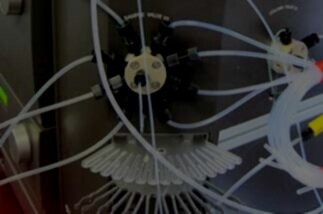