
AKTA Basic, Purifier, and Explorer Service & Repair
You rely on your equipment. Your equipment should rely on ATG.
Analytical Technologies Group specializes in the maintenance and repair of AKTA™ FPLC instruments, including the AKTA™ Basic, AKTA™ Purifier, and AKTA™ Explorer models. We are highly specialized, only servicing a very limited number of instrument lines, so our engineers know these systems every bit as well as the service technicians from the manufacturer. We also keep stock of most parts for AKTA™ FPLCs, to ensure that we’re ready to remedy any problems your system may be having and help keep your FPLC performing well with minimal downtime.
See why over 4,000 customers trust ATG to keep their labs running smoothly.
Tips for keeping your AKTA™ Basic, Purifier, or Explorer in good working order:
Before use each day, inspect the system and pump for leaks. If there is liquid leaking between the pump head and the pump chassis the seals will require replacement..
Check that the volume of rinsing solution in the storage bottle has not changed from the previous use. If it has increased, that could be an indication of internal pump leakage which would require replacement of the piston seals. If the volume has decreased, check the rinsing system connectors. If the rinsing system connectors are mounted properly, the rinsing membranes or piston seals may require replacement.
If your system has a pH electrode, calibrate it before each use.
The system should not be left filled with buffer between uses and should be flushed with purified water after each use. If you are not using the separation unit for multiple days (such as over the weekend), flush the flow path with distilled water, replace the column with a bypass capillary, and replace the pH electrode with the pH dummy electrode). Fill the system with 20% ethanol in distilled water.
The pH electrode should be stored in a 1:1 mixture of pH 4 buffer and 2 M KNO3 when not in use.
Change the rinsing solution weekly. Only 20% ethanol should be used as a rinsing solution.
Check the inlet filters weekly by visual inspection and replace them if they appear dirty.
Replace the on-line filter weekly.
The system should be cleaned monthly by a wash of 1 M NaOH followed by a wash of distilled water. Replace the column with bypass tubing and replace the pH electrode with a dummy electrode before this wash. This should be followed with a 20% EtOH rinse for storage.
Check that the flow restrictor generates the appropriate back-pressure (0.4 ± 0.05 MPa for the FR-904 or 0.2 ± 0.05 MPa for the FR-902). This should be done monthly.
Check the UV-900 monitor cell and optical fiber connectors every three to six months.
Inspect and clean the UPC-900 UV flow cell every three to six months.
Check the mixer M-925 function every six months. The mixer chamber can be tested by placing a magnetic stir bar on top of the mixer housing; it should rotate when the system is in “Run” mode. Check the tubing connectors and replace if needed.
It is recommended to replace the Mixer M-925 chamber every two years.
Remember to calibrate your system pressure transducer whenever your running conditions change or you are unable to maintain 0.00 MPa with no pressure.
If you change the conductivity cell, be sure to perform the temperature calibration and enter a new cell constant.
Having technical problems with your AKTA™ Basic / Explorer / Purifier?
Fast Response
We provide very prompt responses to customers within one business day.
Fast Turnaround
Our field service engineers are expediently dispatched across North America & Europe to fulfill your service request.
Expert Staff
ATG’s highly trained, highly skilled staff ensure your instruments remain in optimal condition.
Parts In Stock
To minimize instrument downtime, we stock virtually all parts for the systems in which we specialize.
AKTA™ Basic / Explorer / Purifier Troubleshooting Tips:
Most common measurement problems, such as baseline drift, ghost peaks, or general noise, are caused by the system being dirty or having air in it. A good first step to eliminate these causes is to clean the system and purge the lines. Ensure all buffers are thoroughly degassed before use.
Noise or instability in UV or conductivity measurements could be caused by air in the flow cells. Check that the flow restrictors are generating the correct back-pressure. If they are not, check the connections to the flow cells and clean the flow cells to purge the air. If the flow restrictors still do not generate the correct back-pressure, you may need to replace the flow restrictors.
Ghost peaks in the UV curve could both be caused by a malfunctioning mixer. Check that it is functioning properly by placing a magnetic stir bar on top of the mixer housing; it should rotate when the system is in “Run” mode. Check that the correct chamber volume is being used.
Conductivity baseline drift can be caused by leaks, improper mixer function, a dirty flow cell, air in the flow cell, or a non-equilibrated column.
Wavy conductivity gradients may be due to pump or valves. Ensure both are operating properly and programmed correctly. Wavy gradients could also be due to the mixing chamber. A larger mixing chamber volume may solve the issue. Check for mixer motor failure as well.
Non-linear gradients or slow response to %B changes could indicate that the mixing chamber is too large. If you are using a larger chamber than the standard 0.6 ml chamber, try downsizing. Tubing which has not been washed properly prior to your run can also cause non-linear gradients, as can a malfunctioning pump.
Incorrect or unstable conductivity readings could be a symptom of a malfunctioning pump, the conductivity flow cell cable not being connected properly, the temperature sensor not being properly calibrated or an incorrect temperature compensation factor, a malfunctioning mixer, or a column which is not equilibrated or dirty.
Problems with the pressure curve could indicate a number of things. There could be air bubbles in the pump, in which case check for leaks and ensure there is sufficient eluent in the reservoirs. The pump valves may not be functioning properly, which may be solved by cleaning. The piston seal may be leaking and in need of replacement. The flow path could be blocked, which may be fixed by flushing it, replacing tubing, and / or filtering your buffers or samples prior to use.
Low eluent flow and noise from the pump likely indicate that piston components need to be replaced. You may need to replace the piston spring (corrosion is a certain indicator it needs replacement), the piston seal, or the piston itself.
If you have erratic pump pressure, use UNICORN™ and observe the piston status indicator and pressure trace to determine which cylinder is functioning abnormally. It may simply have air in it which needs to be purged, or a component may need replacement. If the erratic pressure does not appear to be tied to a particular cylinder, it could simply be a leaking connection.
If a valve is not switching, the connection to the pump may be incorrect or the UniNet cable may need replacement. Also, ensure the ID-switch of the valve corresponds to the ID in UNICORN™.
A valve switching to an incorrect position may indicate that it was reassembled incorrectly.
Any internal leakage from the valve indicates that it should be replaced.
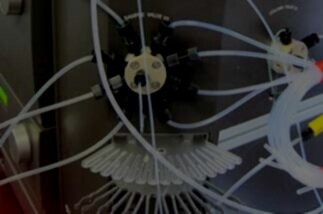